Unidad 6 Mejora Continua
TEMA 9: DESARROLLO DE LA METODOLOG´IA DE TAGUCHI

Off Line y, por tanto, de un diseño apropiado del producto y del
proceso. Este enfoque se basa más en aspectos relacionados con la
infraestructura de la calidad que en aspectos relacionados con la filosofía de
empresa y estadística. Se utilizara fundamentalmente el diseño de experimentos
como herramienta para fabricar productos más robustos y, por tanto, menos
sensibles a los factores de ruido. Es decir, se reducen los efectos de la
variabilidad sobre las características de la calidad del producto y del
proceso. Inicialmente, la aplicación del diseño de experimentos estaba más
dirigida a la optimización de los valores promedio de las características de la
calidad sin tener en cuenta los efectos de la variación.
La filosofía de la calidad de Taguchi se puede resumir en los siete
puntos básicos siguientes
1. Un aspecto importante de la calidad del proceso manufacturado es la
pérdida total ocasionada por dicho producto a la sociedad.
2. En una economía competitiva son necesarias una mejora continuada de
la calidad y una reducción de los costos. Este punto marca una diferencia
fundamental entre las políticas de Japón y Estados Unidos, puesto que las
compañías americanas buscan fundamentalmente la nueva tecnología y la
innovación (métodos para la mejora del proceso y el producto), mientras que las
compañías japonesas enfocan sus objetivos a una mejora gradual, empleando el
diseño de experimentos para determinar los parámetros que permiten reducir los
costos y mejorar la calidad.
Se distinguen:
Tres tipos de costos:
·
· Costos
asociados al diseño del producto.
·
· Costos
de manufacturación.
·
· Costos
de operación.
Estos tres tipos de costos se pueden reducir mediante un uso apropiado
del diseño de experimentos.
3. Un programa de mejora continuada de la calidad incluye una reducción
constante de la variación de las características de la calidad en torno a los
valores nominales o umbrales.
4. La pérdida ocasionada por la variabilidad en el proceso de
fabricación del producto es proporcional al cuadrado de la deviación típica de
la característica de la calidad estudiada respecto al valor nominal.
5. La calidad y el coste final del producto manufacturado dependen en
gran medida del diseño efectuado para el producto y el proceso.
6. La variabilidad del proceso y del producto se puede reducir mediante
el efecto no lineal de los parámetros del producto y del proceso sobre las
características de la calidad.
7. Los diseños de experimentos estadísticos pueden ser utilizados para
identificar el conjunto de parámetros del producto y del proceso que reducen la
variación y, por tanto, mejoran la calidad, la productividad, la fiabilidad del
proceso de manufacturación sus resultados.
2. Control de calidad Off Line y On Line
Según se comentó en el primer tema, se distinguen dos aspectos en el
estudio de la calidad de un producto: La calidad del diseño y la calidad de
conformidad. En la nomenclatura adoptada por la metodología de Taguchi estos
dos aspectos son referidos como calidad Off Line y calidad On Line,
respectivamente.
La calidad Off Line está relacionada con los siguientes puntos:
(i) Correcta identificación de necesidades y expectativas del cliente.
(ii) Diseño de un producto que cubra las necesidades del cliente.
2(iii) Diseño de un producto cuyo proceso de manufacturación sea
consistente y económico.
(iv) Desarrollo de especificaciones, procedimientos y equipos de
manufacturación que sean adecuados.
En el proceso que acompaña a la definición de la calidad Off Line hay
dos etapas:
· Diseño del
producto.
· Diseño del
proceso.
En la etapa (I), un nuevo producto es elaborado, o bien un producto
existente es modificado. El objetivo en esta etapa es, según se ha comentado
anteriormente, crear un producto que cubra las necesidades del cliente y que
haga sencillo el proceso de manufacturación.
En la etapa (II), se crean los elementos necesarios para que el proceso
de
Manufacturación permita la elaboración de productos con los
requerimientos y especificaciones establecidos en la etapa anterior. Más
concretamente, los puntos (i)-(iii) son considerados en la etapa Off Line-(I),
mientras que el punto (iv) es considerado en la etapa Off Line-(II). En la
metodología de Taguchi se distinguen tres etapas en el diseño de la calidad Off
Line:
· Diseño del
sistema.
· Diseño de los
parámetros.
· Diseño de la
tolerancia.
Taguchi (1986) establece dos etapas en el control de la calidad On Line:
·
Métodos de control de la calidad de la
producción:
·
· Proceso
de diagnóstico y ajuste.
·
· Predicción
y corrección.
·
· Medición
y acción.
·
· Relaciones
con los clientes.
A continuación se describen las etapas señaladas en la metodología de
Taguchi para el control de la calidad.
Calidad Off Line
En la etapa (I), es decir, en el diseño del producto, se considera en
primer lugar el problema de diseño del sistema. Se aplica entonces el
conocimiento científico para desarrollar un prototipo de diseño que cumpla los
requerimientos del cliente. La selección inicial de materiales y de
tecnología para el proceso de manufacturación es realizada en esta fase.
El principal objetivo en esta etapa es conseguir la mejor tecnología disponible
para cubrir las necesidades del cliente al costo más bajo posible. Este ´último
aspecto diferencia la metodología de Taguchi de la metodología Western, donde
el objetivo prioritario es el uso de la ´ultima tecnología, aunque esto suponga
aumentar los costos. El siguiente paso es el diseño de los parámetros,
determinando el conjunto ´óptimo de parámetros del producto. El objetivo aquí
es minimizar los costos de manufacturación y de la vida del producto mediante
minimización de la variación en la ejecución. Esto se consigue mediante la
creación de diseños robustos, que no se ven afectados por los factores de
ruido. Un factor de ruido es una fuente de variación incontrolable en las
características funcionales del producto. En esta etapa de diseño de los
parámetros se utiliza el diseño de experimentos para determinar el impacto de
los factores controlables y no controlables (ruido) sobre las características
del producto. El objetivo aquí es la selección de niveles de los factores
controlables que permiten minimizar los efectos de los factores de ruido,
haciendo el producto robusto frente a dichos factores.
Finalmente, en el diseño de las tolerancias se establecen los límites en
torno al valor nominal o umbral establecido en la etapa anterior. El objetivo
en esta etapa es definir o especificar unas tolerancias lo suficientemente
amplias como para minimizar costos, pero manteniendo las características
funcionales del producto dentro de las especificaciones.
En la etapa (II), es decir, en el diseño del proceso, se considera, en
primer lugar, de forma paralela a la etapa anterior, el diseño del sistema, que
consiste en la selección del proceso de manufacturación sobre la base del
conocimiento del producto y de la tecnología de manufacturación de ese momento.
El objetivo principal es especificar el uso de maquinaria existente y el
proceso en la medida de lo posible.
En el diseño de los parámetros se determinan los niveles apropiados de
los factores controlables que intervienen en el proceso de producción. El
objetivo aquí es hacer el proceso robusto para minimizar los efectos de ruido
sobre el proceso de producción y el producto acabado. El diseño de experimentos
es utilizado durante este paso.
Finalmente, en el diseño de las tolerancias, se establecen las
tolerancias para los parámetros del proceso, identificadas como críticas en el
diseño durante el diseño de los parámetros. Si el diseño de los parámetros del
proceso o del producto se ha realizado pobremente, es necesario, quizás,
realizar un reajuste de tolerancias, o bien considerar materiales de elevado
costo o equipos de alta calidad, lo que produce un incremento de los costos de
manufacturación.
42.2. Calidad On Line
En la metodología de Taguchi se distinguen tres vías para el control de
la calidad On Line:
Diagnóstico y ajuste del proceso: El proceso es examinado en intervalos
regulares de tiempo; ajustes y correcciones son efectuados según las
necesidades que surgen.
Predicción y corrección: Un parámetro cuantitativo o numérico del
proceso se mide en intervalos regulares de tiempo. Los datos son utilizados
para proyectar tendencias en el proceso. En el caso en que el proceso se
encuentra demasiado alejado de los valores umbrales o nominales, el proceso es
reajustado para corregir la situación.
Este método se conoce con el nombre de control feedback o feedforward.
Medición y acción: Consiste en el control de la calidad mediante
inspección. Cada unidad manufacturada es inspeccionada. Las unidades
defectuosas son reparadas o eliminadas. Este procedimiento de control de la
calidad es el más caro, puesto que no previene defectos ni tampoco identifica
todas las unidades defectuosas.
Relaciones con los clientes: Servicios a clientes pueden ofrecer la
reparación o el reemplazamiento de productos defectuosos, o bien la
compensación de pérdidas.
Se puede actuar sobre los tres tipos de factores de ruido que se
consideran en la
Metodología de Taguchi, es decir, factores de ruido externo, interno y
unidad a unidad, en diferentes etapas del proceso, no solo en el diseño de los
parámetros asociado al control de la calidad Off Line. Por ejemplo, se puede
actuar sobre los tres tipos de ruido en el diseño del producto, en las etapas
de diseño del sistema y de diseño de los parámetros. En el diseño de las
tolerancias solo se puede actuar sobre factores de ruido interno y unidad a
unidad. Sobre estos ´últimos factores de ruido también se puede actuar desde la
fase de diseño del proceso. Con el control de la calidad On Line también se
puede actuar sobre los factores de ruido unidad a unidad.
FUNCIÓN DE PÉRDIDA
La calidad del producto ha sido medida usualmente mediante comparación
de características críticas del producto con especificaciones de fabricación
establecidas para el producto. Las especificaciones sobre el producto son
importantes. Sin embargo, en la actualidad hay un interés creciente por el
desarrollo de técnicas que permitan el control de características del
proceso que determinan la calidad del producto final. El objetivo final es
reducir la variabilidad del proceso y conseguir que las características de la
calidad se encuentren lo más cercanas posibles a los valores umbrales. Las
especificaciones en el proceso de fabricación suelen venir dadas en
términos de la cantidad de variabilidad que puede ser tolerada en las características
del producto y del proceso. Normalmente suelen ser expresadas en términos
de: Un valor estándar o umbral.
Límites de tolerancia bilaterales (naturales o especificados). Valores
umbrales con un rango de tolerancia (natural o especificado). Límites de
tolerancia unilaterales (superiores o inferiores). Según nos alejamos del valor
umbral la pérdida aumenta. Por tanto, en el diseño de una función de pérdida se
ha de considerar una función cuyo mínimo se encuentre en el valor umbral u
objetivo y cuyos valores aumenten progresivamente según nos alejamos de dicho
valor. En particular, es deseable un incremento de la velocidad de crecimiento
de los valores de la función de pérdida a partir de los puntos definidos por
los límites de tolerancia (asíntotas verticales situadas sobre los límites de
tolerancia). La función dependida puede ser simétrica o asimétrica. En la
metodología de Taguchi se utiliza una función de pérdida L cuadrática, según se
vio en el Tema
Según este modelo, la pérdida es causada por la variabilidad de la
característica estudiada y por el sesgo. Por tanto, para reducir la pérdida se
debe actuar sobre la variabilidad del proceso y sobre la desviación del valor
medio de la característica de la calidad estudiada respecto al valor nominal.
Este argumento será utilizado también, en la próxima sección, para justificar
el uso de la razón señal- ruido en la fase de diseñó de los parámetros.
RAZONES SEÑAL RUIDO
Tradicionalmente, mediante técnicas de diseñó de experimentos se han
evaluado los efectos de factores sobre la calidad de una característica. En el
caso de una sola realización para cada experimento, se combinan los diferentes
valores de la respuesta observados en cada realización de los experimentos,
definidos en la matriz del diseñó, para obtener una estimación de los efectos
principales y de sus interacciones. Cuando se consideran réplicas de la
variable respuesta en cada combinación de los niveles de los factores, la
variación del error también puede ser estimada; el análisis se define en
términos de los valores medios muéstrales obtenidos de las réplicas.
Sin embargo, cuando se introduce la función de pérdida (en particular,
cuando se considera la formulación se hace patente la necesidad de
combinar el estudio de la respuesta media con la variabilidad, es decir,
definir una medida que recoja ambos aspectos. Esta medida es referida por
Taguchi como razón señal- ruido. Esta terminología proviene del lenguaje
utilizado en ingeniería, donde la media de la variable respuesta representa la
señal y la variación σ
Representa el ruido. Se pueden definir diferentes medidas de razón
señal- ruido, dependiendo del objetivo del estudio. Las más frecuentes son:
(Aproximación a un valor nominal. La pérdida se incrementa según la
característica de la calidad estudiada se aleja del valor nominal. Aproximación
al valor más pequeño. El valor nominal es cero y la característica de la
calidad es no negativa. La pérdida disminuye según la característica de la
calidad se aproxima a cero.
Aproximación al valor más grande. El valor nominal es infinito y la
característica de la calidad es no negativa. La pérdida disminuye cuando la
característica de la calidad crece. En el caso, se considera un factor o
parámetro de ajuste que elimine el sesgo de la variable respuesta o característica
de la calidad estudiada. Los parámetros de ajuste son factores controlables
sobre los que se puede actuar. En algunos casos, se pueden determinar
parámetros de ajuste que modifiquen la media sin afectar a la varianza.
Mediante el uso de dicho parámetros, se consigue eliminar el sesgo o reducirlo
considerablemente. La pérdida media viene dada entonces en términos de kσ2 y el
objetivo será minimizar o reducir la variabilidad.
5. Diseño de experimentos ortogonales
Para el estudio de los factores que afectan a un producto o proceso,
Taguchi se basa en un conjunto pequeño de matrices del diseñó. Estas matrices
definen diseños ortogonales, es decir, sus columnas son ortogonales. Los
diseños factoriales 2k son un ejemplo de diseños ortogonales. Taguchi utiliza
los valores 1 y 2 para denotar los niveles bajo y alto, respectivamente, en
lugar de la notación usual ±, puesto que considera la posibilidad de más de dos
niveles en cada factor. En la metodología de Taguchi se consideran diseños
ortogonales fraccionarios, es decir, se reduce el número de filas de la matriz
del diseñó mediante identificación de factores principales y de factores de
interacción. Esto permite una mayor viabilidad del estudio de tratamientos. Por
ejemplo, para el diseñó 27 de 7 factores con dos niveles, Taguchi considera la
siguiente matriz de diseñó:
6.2 FUNCIÓN DE PÉRDIDA DE LA CALIDAD
La función de perdida de la calidad, comúnmente llamada función de
perdida de Taguchi (por su creador Genichi Taguchi, en la segunda mitad del
siglo .XX), es una herramienta de cálculo usada en ingeniería para el control
de calidad. Esta herramienta sirve para evaluar de forma numérica la “pérdida
de calidad” en un proyecto, producto o servicio, con respecto a su nivel de
calidad óptimo.
La idea fundamental de las metodologías creadas
por Genichi Taguchi es poder diseñar y fabricar productos en poco tiempo con
alta calidad, evitando tener que usar el método de prueba y error, que es más
caro y lento. Para conseguir estas mejoras, se intentan optimizar los
diseños de los productos y de los procesos de fabricación a través de la
ingeniería de calidad y la estadística.
La función de pérdida de la calidad de Taguchi nos ofrece una forma de
calcular la “pérdida de calidad” que sufre un aspecto analizado con respecto al
objetivo de calidad que le hayamos fijado al mismo. Esto significa, que para
una característica fijada en nuestro producto o proceso, la función de
pérdida nos dirá cuándo nos estamos alejando de nuestro objetivo.
La función de perdida es la siguiente:
L = K * (Y – M)^2
Donde…
L es el resultado de la función, medido generalmente en unidades monetarias.
Y es el valor ideal de la característica analizada (nuestro objetivo a alcanzar para ese parámetro). M es la media de valores obtenidos de la característica analizada en la situación real. K es una constante que se encarga de convertir (Y – M)^2 a unidades monetarias.
L es el resultado de la función, medido generalmente en unidades monetarias.
Y es el valor ideal de la característica analizada (nuestro objetivo a alcanzar para ese parámetro). M es la media de valores obtenidos de la característica analizada en la situación real. K es una constante que se encarga de convertir (Y – M)^2 a unidades monetarias.
Por lo tanto, si para una característica analizada, el valor L es de
cero, significará que la calidad obtenida es la calidad deseada (nuestro
objetivo). Si L es mayor que cero, entonces significa que nos estamos alejando
del objetivo.
Por ejemplo, si la característica analizada (tiempo de producción,
tiempo de entrega, coste…) queremos que sea Y=30unids., pero en la práctica
estamos midiendo que de media es M=35unids., y esta desviación (al cuadrado)
supone un coste de K=5€/unid.^2, entonces L=5*(35-30)^2, o sea L=125€. Conviene
tener en cuenta que al haber una resta al cuadrado el valor de L siempre será
mayor igual de cero, que Y-M crecerá cuadráticamente y que K debe ser expresado
en las unidades coherentes.
En el diseño y fabricación de un producto todos los parámetros de
este y de su proceso de fabricación deben estar controlados .Una desviación en
estos parámetros supone una pérdida en la calidad, por ello debemos manejarnos
en unos rangos donde el producto sea válido, es decir, poder fluctuar en
rangos de acción donde dentro de los mismos el producto cumpla las
características que se especifican. Para ello, puede ser importante definir
cuáles son los parámetros clave donde se pueden dar con mayor facilidad
las pérdidas de calidad, y tener más controlados estos parámetros clave.
es decir, analizar si L = K * (Y – M)2 es cero o si es un valor alto,
para posteriormente ver qué causa dicha pérdida de calidad buscando el problema
raíz. El siguiente paso es hacer una interpretación de los resultados
obtenidos, de este modo podemos hacer una valoración global de las pérdidas de
calidad a nivel económico e implantar soluciones para minimizar estas pérdidas
a medida de lo posible.
PARA TAGUCHI, LA PÉRDIDA INCLUYE:
Los costos incurridos por no cumplir el producto con las expectativas
del cliente los costos por no cumplir el producto con las características de
funcionamiento, y los costos causados por los efectos peligrosos secundarios
causados por el producto En las empresas de manufactura, la Función Taguchi de
Pérdida también se puede aplicar en el "cumplimiento de la
especificaciones" de un producto
El Dr. Genichi Taguchi desarrolló en Japón un método aproximado para
calcular las pérdidas que ocasiona a la sociedad un producto de mala calidad.
En su definición de la calidad deja claro este concepto: “Calidad es la pérdida
que un producto causa a la sociedad después de embarcarlo”
PARA TAGUCHI, LA PÉRDIDA DE LA SOCIEDAD INCLUYE;
· Los costos
incurridos por no cumplir el producto con las expectativas del cliente.
· Los costos por no
cumplir el producto con las características de funcionamiento, y
· Los costos
causados por los efectos peligrosos secundarios causados por el producto. En
las empresas de manufactura, la Función de Pérdida también se puede aplicar en
el "cumplimiento de las especificaciones" de un producto.
FACTORES DE RUIDO.
• Causan que una característica
funcional se desvié de su valor objetivo.
• Los factores de ruido causan
variación y pérdida de calidad.
• Taguchi ha observado que esta
pérdida de calidad constituye una pérdida de tiempo y dinero tanto a los
consumidores como a los fabricantes y en ultimo termino a la sociedad
EL OBJETIVO DE LA FUNCIÓN DE PÉRDIDA DEL DR. TAGUCHI
· es evaluar
cuantitativamente la pérdida de calidad debido a variaciones funcionales.
· Para cada
característica de calidad existe una función que define la relación entre la
pérdida económica y la desviación de la característica de calidad de su valor
meta.
ES IMPORTANTE RECORDAR.
• Conformarse con los límites de la
especificación es un indicador inadecuado de calidad o de perdida debido a la
mala calidad.
• La pérdida de calidad resulta en la
inspección del consumidor.
• La pérdida de calidad se relaciona
con las características del producto.
• La pérdida de calidad es una
pérdida financiera.
• La función de perdida es una
herramienta excelente para evaluar la perdida en la etapa inicial del
desarrollo de productos y procesos.
EJEMPLO:
Pieza critica del sistema de frenos de un automóvil. Todos los productos
se inspeccionan al 100 %. El costo es el mismo en cualquiera de las fábricas.
¿Cómo consumidor, que fabrica escogería usted? ¿Por qué?
En cual fabrica se da la mayor variación. Que fabricas tienen la misma
variación
Función de pérdida para una característica del tipo:
Nominal es mejor.
Se expresa con la siguiente ecuación:
L(y) = K(y-m)2
L (y) = Pérdida en dinero por unidad de producto cuando las
Características de calidad son iguales a y.
· y = Valor de la
característica (longitud, anchura, etc.)
· m = Valor nominal
de y.
· K = Constante de
proporcionalidad.
· L (y) = Es mínima
cuando y=m
· L (y) = Aumenta
en la medida en que y se desvía de m.
· L (y)= Se expresa
en unidades monetarias
Ejemplo: Nominal es mejor.
Se fabrican aparatos de televisión con los valores nominales deseados
para un voltaje de salida m= 118 volts, cuando el voltaje de salida adquiere un
rango de ± 25 volts el costo promedio para reemplazarlo o reparar el aparato es
de $ 185.
6.3 MODELO KAIZEN
LA CLAVE DE LA VENTAJA COMPETITIVA JAPONESA DE MASAAKI IMAI
Todo comenzó en los sistemas de producción de las empresas japonesas de
automoción, cuando empezaron a utilizar estrategias, métodos y herramientas de
mejora que les proporcionaron una forma de trabajar que permitía mantener una
producción flexible, aumentando la calidad y todo ello, con enorme ahorro de
costes.
La palabra Kaizen proviene de la unión de dos vocablos japoneses: KAI
que significa cambio y ZEN que quiere decir bueno o bondad. Analizando
ambos significados conjuntamente podemos empezar a deducir cual es el núcleo de
esta filosofía, el espíritu de la: MEJORA CONTINUA.
Tal como lo describe Massaki Imai “Kaizen significa mejoramiento
continuo que involucra a todos, tanto a gerentes como a trabajadores”.
KAIZEN.
Kaizen es una filosofía, una manera de pensar y se basa en ciertas
herramientas o prácticas administrativas que se creían exclusivamente japonesas
y que han alcanzado fama mundial. Esta filosofía nos dice que nuestra forma de
vida sea laboral, social o familiar, debe y merece ser mejorada constantemente.
Este mensaje de Kaizen es que “No debe pasar un día sin que haya hecho
alguna clase de mejoramiento en algún lugar de la empresa”. Significa un
esfuerzo constante, no sólo para mantener los estándares, sino para mejorarlos.
Requiere de los esfuerzos de todos y se interesa más en el proceso que en el
resultado.
El modelo Kaizen plantea entonces que para analizar los problemas de una
organización no se debe ver el nivel de producción pues ese es solo una medida
y lo que importa es el proceso. El modelo occidental, en la generalidad, se
fija únicamente en la evaluación de resultados lo que limita su competitividad
y su capacidad para mejorar continuamente. Cuando el Kaizen es parte de la
cultura de la organización, se espera que ocurra por lo menos en bases diarias
de todos los empleados. Las mejoras no son esperadas como cambios masivos, sino
por pequeñas y frecuentes ideas que son impulsadas.
VALORES.
Se hace uso de una serie de sistemas, técnicas, metodologías y
herramientas destinadas a lograr cada día mejorar las distintas performances.
· Orientación
al cliente.
· Control
Total de Calidad.
· Robótica.
· Círculos
de Control de Calidad.
· Sistemas
de Sugerencias.
· Automatización.
· Disciplina
en el Gemba.
· TPM.
· Layout.
· Desarrollo
de nuevos productos.
· Kanban.
· Just
in Time.
· Funcion
de Perdida de Taguchi.
· Poka
Yoke.
· Andon.
· Cero
Defectos.
· Actividades
de Grupos Pequeños.
· QFD.
· AMFE.
|
Para Kaizen la administración establece el Procedimiento Estándar de
Operación (PEO): políticas, reglas, directrices, procedimientos y disciplina;
luego toda la organización sigue el PEO formulado.
EL KAIZEN Y LA INNOVACIÓN.
Kaizen significa mejoras pequeñas realizadas en el
“status quo” como resultado de los esfuerzos progresivos.
La Innovación implica una mejora drástica en el “status
quo” como resultado de una inversión más grande en nueva tecnología y (o)
equipo.
Habiendo dos enfoques de progreso el gradual y el salto
hacia delante, Kaizen es de tipo gradual, mientras que el modelo occidental
privilegia la innovación como método de salto hacia delante.
El proceso de innovación occidental tiende a ser como
una escalera que genera mejoras progresivas de manera esporádica, pero que
sin un esfuerzo constante de mantención el progreso logrado declina con el
tiempo.
El proceso de Kaizen considera un esfuerzo constante
para generar una mejora continua en una suma de pequeños logros.
|
Para el Kaizen, el mantenimiento implica todas aquellas
actividades dirigidas a conservar los actuales estándares tecnológicos,
administrativos y de operaciones.
IMPORTANCIA DE LOS ROLES.
El éxito del Kaizen en las organizaciones se relaciona directamente con
el pensamiento y cultura de la organización. Las ideas originales para el
kaizen, comenzaron en Japón. Ahora, la idea de que las mejoras es
continua, es tan intrínseco dentro de la sociedad japonesa que se ha convertido
en un modo de vida. Las mejoras Kaizen son parte normal de difusión, en cada
conversación y hasta en los libros de los niños. Kaizen o mejoramiento,
es un modo de pensar y reaccionar tanto dentro como fuera del ambiente de
trabajo. El tipo de pensamiento ha estado firmemente implantado no solo en los
ambientes de trabajo japoneses, sino que también en la sociedad japonesa.
En contraste, con la responsabilidad para mejorar en plantas
manufactureras tradicionales por lo regular recae con seguridad en la
administración, no con la fuerza de trabajo entera. En general, los
administradores asumen la responsabilidad para las mejoras; ellos no piensan
acerca del involucramiento de otros empleados en sus procesos de mejora.
De hecho, el rol del administrador, como tradicionalmente se define,
desalienta el involucramiento por no administración personal. En general, otros
en la organización no piensan en ofrecer sugerencias como parte del trabajo de
alguien más. Sin embargo, si no todos desean hacer sugerencias, los caminos
para estas no existen. Cuando las mejoras son hechas, el administrador
ordinariamente toma las mejoras por entendidas, a pesar de que las mejoras
fueron realizadas por el administrador o por otros. Estos cambios aleatorios y
el carecimiento de la importancia puesta en ellos, usualmente resulta en la
compañía solo para guardar el status quo.
¿Por qué las mejoras son conmiseradas como trabajo de los
administradores? En la manufactura tradicional, las actividades de mejora no
están puestas como superiores en las lista de importancia. Las metas anuales de
los gerentes usualmente no incluyen una mención del número de pequeñas mejoras
realizadas este año por el contrario, las recompensas de los gerentes son
proveídas cuando la producción está a tiempo y su costo es mínimo. Los
resultados base comienzan a ser las medias básicas del éxito de un gerente.
Lo opuesto es una realidad en Kaizen en un ambiente
esbelto de producción. El Kaizen es considerado como la tarea más importante
del administrador. De hecho, entre más alto este el administrador, más Kaizen
es parte de su trabajo. En un ambiente Kaizen, cada uno entiende claramente y
espera todo de sus administradores.
Si este es el caso, el desarrollo de una nueva cultura puede empezar con
algunos estándares para administración y el lugar de trabajo. Este cambio
cultural puede incluir el desarrollo de:
· Empleados quienes
entienden los estándares de trabajo y la filosofía Kaizen.
· Relación de
trabajo fuerte de los gerentes a los empleados así como de los empleados a los
gerentes.
· Gerentes se
convierten en líderes fuertes quienes son altamente hábiles en los procesos del
trabajo.
· Empleados quienes
son altamente hábiles y conocen su proceso de trabajo.
· Recompensas de
los administradores basados en las actividades kaizen y en las relaciones
positivas establecidas con los empleados.
· Procedimientos
claros y reglas de trabajo.
Claramente los cambios se requieren en una cultura de la manufactura
para realizar la aceptación de las actividades Kaizen como parte de una vida de
trabajo diaria para todos los empleados. Un grupo administrativo fuerte con un
enfoque en la mejora continua es un comienzo. La importancia de los roles está
altamente conectada con el involucramiento de cada empleado.
PASOS PARA IMPLEMENTAR EL KAIZEN.
Antes de lanzar cualquier forma de Kaizen dentro de un ambiente de
trabajo, las decisiones acerca de una estrategia para Kaizen deben ser
decididas. Tres pasos básicos son necesarios. Primero, es una necesidad contar
con un plan para la introducción e implementación del Kaizen. Segundo, los
empleados deben ser proveidos con conocimientos de los procesos de Kaizen.
Tercero, deben ser aprendidas por todos los empleados simples pero efectivas
habilidades en la solución de problemas.
· Paso 1:
Desarrollo e implementación de un plan
Primero, un plan debe ser creado para la implementación de las
actividades Kaizen. Para crear este plan, muchas preguntas deben ser
contestadas. ¿Cuál forma (s) de kaizen debe ser adoptada? ¿Cuáles son los
resultados esperados? ¿Cómo puede el Kaizen ser introducido exitosamente en el
ambiente de la fábrica? ¿Qué es lo que se concluye en los procesos Kaizen?
¿Cómo pueden las expectativas ser comunidades exitosamente? Por ahora, el
enfoque será planear de manera general las actividades del Kaizen contestando
las preguntas.
Tres pasos básicos son necesarios:
· Primero, es una
necesidad contar con un plan para la introducción e implementación del Kaizen.
· Segundo, los
empleados deben ser proveídos con conocimientos de los procesos Kaizen.
· Tercero, deben de
ser aprendidas por todos los empleados simples pero efectivas habilidades en la
solución de problemas.
El soporte de la alta gerencia es esencial. Para este soporte, la
planeación y el monitoreo continuo de los procesos Kaizen es mejor regulado a
través de un comité directivo de la alta gerencia. Sin este comité de la alta
gerencia, el soporte para los procesos posiblemente estará limitado.
El propósito de este comité es:
· Establecer metas
y comunicar los resultados esperados de las actividades Kaizen.
· Alcanzar en bases
regulares el monitoreo del progreso de las actividades Kaizen a través de
juntas regulares.
· Dar soporte a los
grupos Kaizen atendiendo a las juntas Kaizen en bases regulares.
· Mejorar y
redefinir los procesos Kaizen, como se necesite.
En adición al comité directivo, una persona debe ser designada como
coordinador de tiempo completo para las actividades Kaizen.
El coordinador deberá:
· Escribir la
documentación explicando el intento de las actividades Kaizen.
· Programar en
bases regulares las juntas del comité directivo.
· Reportar las
actividades Kaizen al comité directivo.
El coordinador podría también planear la introducción de actividades de
la planta, entrenar empleados en habilidades Kaizen, supervisar las actividades
Kaizen y facilitar los cambios en los procesos Kaizen.
La implementación de un proceso Kaizen a lo largo de la compañía
requiere tanto tiempo como tenacidad. El Kaizen es un proceso que se convierte
en un modo de vida dentro de la organización. Los miembros del comité directivo
y el coordinador del Kaizen deben entender que se requiere tiempo considerable
al inicio de estas actividades tanto como coordinación perpetua del procesos
Kaizen.
Los planes deben ser hechos para comunicar el proceso Kaizen a todos los
empleados. A la mayoría de los empleados no se les ha pedido contribuir a las
mejoras de la compañía. De hecho, de alguna manera, lo contrario puede ser
cierto. Los empleados quizás hayan sido desalentados al ofrecer sugerencias.
Así, los empleados probablemente no entenderán inmediatamente la motivación de
la empresa en involucrarse administrativamente en las actividades de mejora
continua. Si no existe historia de la planta en la cual incluya a todos los
empleados en un proceso de mejoramiento, es importante explicar el significado,
la necesidad y los resultados esperados para las actividades Kaizen en las
cuales ellos participan.
Una decisión importante que debe realizar el comité directivo involucra
los tópicos específicos a ser establecidos a través de los procesos Kaizen.
¿Cuáles tópicos serán considerados en el Kaizen y cuáles no estarán asentados a
través del Kaizen?
El enfoque del Kaizen debe claramente ser la mejora de los procesos de
manufactura y de las actividades relacionadas a estos procesos. Los empleados
que dirijan las iniciativas Kaizen usualmente incluyen sugerencias tales como
la mejora de la calidad o ahorros relacionados a sus áreas de manufactura. Las
actividades que fueron señaladas sin intervención usualmente incluyen las
decisiones gerenciales tradicionales. Por ejemplo, los empleados no podrían
determinar las políticas de las compañías.
Las iniciativas dirigidas por el equipo, usualmente incluyen mejoras en
los procesos de producción, las sugerencias para mejorar la calidad, e ideas en
mejoras a las maquinas. La importancia de hacer una clara distinción desde
inicios de los procesos puede ser tomada como entendida. Los empleados deben
ser alejados de los problemas no-Kaizen, de otra manera cuando las actividades
son seleccionadas como un tópico Kaizen, el riesgo de los procesos Kaizen
comenzaría a ser visto como un límite injusto.
Un plan para lo esperado de las actividades Kaizen es necesario que se
ajuste con las metas expectativas para la empresa. Este plan debe ser claro y
conciso. Específicamente ¿Qué espera la empresa que hagan los empleados? ¿Qué
está incluido para los empleados cuando ellos hacen sugerencias o completan
proyectos Kaizen?
Por otra parte, es extremadamente importante no sobre-prometer
resultados a los empleados. Explicando que el proceso Kaizen es un proceso
continuo largo, es un buen inicio. Esta explicación puede comenzar con un
entrenamiento introductorio para estos empleados.
· PASO 2.
ENTRENANDO A LOS EMPLEADOS
Una vez que las actividades Kaizen han sido introducidas a los
empleados, el siguiente paso es entrenar a los empleados a seguir los procesos
Kaizen y los beneficios de contribuir a los procesos. Los objetivos para el
entrenamiento deben incluir:
· Conocimiento
general en los procesos Kaizen.
· Clara definición
de los roles.
· Resultados
esperados del proceso.
· Desarrollo de
habilidades de comunicación en el equipo.
· Guías, tales como
el pago por el tiempo de juntas.
En este punto, entrenamiento en habilidades específicas para los
empleados debe ser también necesario. Es difícil para los empleados hacer
sugerencias si ellos no entienden los procesos de manufactura que se encuentran
alrededor de su trabajo. También es buena idea proveer conocimientos generales
de los procesos debe ser utilizado por los clientes y proveedores internos.
PASO 3. PROVEER HABILIDADES EN LA SOLUCIÓN EN
PROBLEMAS
Ahora que los empleados entienden de manera general los procesos Kaizen
utilizados por su equipo, es tiempo de aprender técnicas para solucionar
problemas. Sin embargo, antes de que los empleados empiecen con los procesos
Kaizen, son necesarios las habilidades en la solución de problemas. Un
pensamiento de solución de problemas debe ser creado para que continuamente
rete a los empleados a pensar mejores formas para realizar el trabajo. Además,
habilidades especificas en la solución de problemas, tales como tabulando
datos, serán necesarios para proyectos del equipo a largo término.
El proceso de solución de problemas aprendido por el Kaizen está puesto
en práctica en las áreas de trabajo con proyectos tales como cambiando de lotes
a flujo de una sola pieza o disminuyendo el tiempo de cambios de modelo.
KAIZEN Y ESTANDARIZACIÓN.
¿Por qué es la estandarización tan importante en los procesos Kaizen? El
trabajo estándar por sí mismo es tan importante porque el proceso escrito que
define claramente las operaciones precisas seguidas por todos los operadores.
Esto es verdad así que el documento es un documento de operación estándar o una
forma de mejora.
En relación con el Kaizen operaciones estándar provee una “fotografía”
mostrando cómo se termina el proceso. Cuando todos los operadores realizan el
procedimiento exactamente, tal como ha sido escrito “estable” porque no hay
variaciones. Cuando las variables no están presentes en el proceso es posible
contar con un producto con alta calidad consistentemente predecible. Cuando los
problemas ocurren en la operación, los problemas pueden ser aislados y
solucionados más fácilmente. Por otra parte, si un proceso no es estable, la
causa del problema no puede ser identificada con certeza.
A través de los procesos Kaizen las mejoras serán hechas tales como
cambios en los procesos de producción y arreglos en el área de trabajo.
Pequeñas ideas provenientes del equipo, serán llevadas a cabo en bases diarias.
¿Cómo pueden estos cambios ser comunicados en el equipo y de turno a turno?
¿Qué procesos pueden ser usados para conservar estas nuevas mejoras de que no
se pierdan a través del tiempo? De nuevo, la estandarización es la respuesta.
Si las nuevas mejoras afectan un cambio en la operación estándar, las
hojas de operación estándar deben ser actualizadas. Los nuevos estándares ya
sea que reemplacen o sean agregados los documentos estándares de operación. Los
documentos escritos llamados hojas de operación estándar, describen los pasos
exactos utilizados para analizar el proceso. Durante las operaciones de
producción estos pasos son seguidos exactamente por el operador. Sin embargo,
las hojas de operaciones estándar deben ser actualizadas solo después de que
hayan sido seguidos los procedimientos oficiales de aprobación.
Para procesos no productivos, un documento de comunicación estándar debe
ser desarrollado y utilizado para cada cambio. También se necesita un procedimiento
de aprobaciones para informar a todos los miembros del equipo afectados por el
cambio.
Hay otras razones para actualizar las hojas de operaciones estándares
una vez que las mejoras son hechas. Cuando nuevas ideas son introducidas la
gente tendrá la tendencia de querer usar los procesos viejos o más familiares.
Es fácil continuar usando los estándares viejos. Sin embargo, con los nuevos
procesos escritos para que todos los usen, la nueva idea es clara y precisa,
haciéndolo menos abierto a la interpretación. Una vez escrito, se espera que
todos realicen los procesos de la misma manera. Cambios variables de realizar
el trabajo no es aceptable. Además, cuando la nueva idea está escrita, es menos
probable que la nueva idea se pierda a través del tiempo. Una forma simple y un
proceso simple, deben ser desarrollados para capturar estas ideas en un formato
estándar. Por lo regular documentación escrita a mano es rápida y aceptable.
CUATRO FORMAS DEL KAIZEN.
Hace algunos años, un empleado de Eastman Kodak, Allan Mogensen, estuvo
pensando cómo mejorar el movimiento en el lugar de trabajo. Mogensen video
grabo a los operadores de producción y escucho como los empleados discutían sus
procesos de trabajo. Cuando el escucho a sus operadores, Mogensen hizo un
descubrimiento. Los trabajadores conocían su trabajo muy bien y cada uno tenía
buenas ideas acerca de cómo hacer su mejor trabajo.
Desde estas lecciones, está claro el viejo dicho: “Dos cabezas son
mejores que una”, es verdad. Algunas personas trabajando juntas para un
propósito en común mejoran sus procesos de trabajo desde el punto de Kaizen.
El Kaizen puede ser utilizado al referirse a cualquiera de sus cuatro
formas: círculos de calidad, eventos kaizen, mejoras diarias y sistemas de
sugerencia. Cada tipo de Kaizen es explicado más adelante. Para que cualquiera
de esas formas de Kaizen sea exitosa, lo siguiente debe ser llevado a cabo.
· Un sistema paso a
paso debe ser establecido para discutir tanto las ideas como la manera en que
deben ser llevadas a cabo.
· Todos deben
entender el sistema.
· El tiempo y
algunos fundamentos deben estar disponibles.
· Soporte constante
debe ser mostrado para las ideas Kaizen.
· El Kaizen debe
empezar a ser parte de la cultura de manufactura.
· Alguna forma del
entrenamiento del equipo debe ser proveída para instruir a los empleados en
cómo comunicarse en el ambiente de equipo.
MEJORAS DIARIAS.
Todos tienen inspiraciones de cómo hacer las cosas mejor en los lugares
de trabajo. Sin embargo, una manera de exponer soluciones en la práctica
usualmente no existe. A través de un sistema conocido como “mejoras diarias” es
una manera rápida, simple para capturar aquellas ideas que son proveídas. Las
mejoras diarias son pequeñas, cambios día a día concebidos y completados por
cada empleado. Un ejemplo de una idea que podría caer bajo esta categoría de
mejoras diarias es el mover el contenedor en la línea de producción a una
posición más alta para que el operador no se tenga que inclinar mucho. Como se
muestra en este ejemplo, una mejora diaria es usualmente un cambio pequeño
relacionado con el área de trabajo de la persona o del equipo.
Siguiendo unos pocos de pasos simples, estas pequeñas ideas pueden ser
implementadas. Cuando un empleado tiene una sugerencia, la idea es discutida
verbalmente con los compañeros y con el supervisor. Debe ser claramente
definido quien exactamente debe ser consultado. Si la idea es aprobada, los
empleados implementan la idea. Note que los empleados son los responsables
desde principio a fin. El empleado concibe la idea, comunica a todos los
involucrados, obtiene la aprobación e implementa la idea.
La diferencia básica entre las mejoras diarias, círculos de calidad y el
sistema de sugerencia es la magnitud de las ideas. Las mejoras diarias son
pequeñas y menos difíciles de alcanzar. El sistema de sugerencias de ideas y
6.4 LAS 9´S
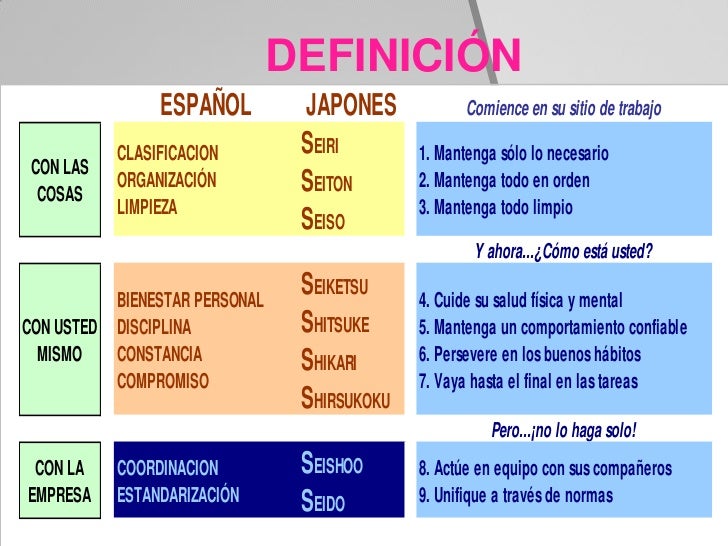
METODOLOGÍA DE LAS 9S
· Un poco de
historia… Shigeo Shingo (Saga, Prefectura de Saga, Japón 1909 – 1990) fue un
Ingeniero Industrial japonés que se distinguió por ser uno de los líderes en
prácticas de manufactura en el Sistema de Producción Toyota. Durante la década
de los 40’, Shingo estudió y aplicó el Control Estadístico de la Calidad. Junto
a Taiichi Ohno inventaron el sistema Just in Time. Entre otros desarrollos
también se encuentra el SMED, los Poka Yoke (sistema de inspección en la
fuente) entre otras aportaciones. Si bien, es reconocido como el creador de la
metodología de las 9S.
¿QUÉ SON LAS 9S?
· Es una
metodología que está evocada a entender, implantar y mantener un sistema de
orden y limpieza en la organización. Los resultados obtenidos al aplicarlas se
vinculan a una mejora continua de las condiciones de calidad, seguridad y medio
ambiente.
CONCEPTO
· “Las 9 “s” deben
su nombre a la primera letra de la palabra de origen japonés; el significado de
cada una de ellas será detalladamente analizado, así como el procedimiento para
llevarlas a cabo además de las ventajas que conlleva realizarlas.” Con la
implementación de las 9 “s” se pueden obtener los siguientes resultados: — Una
mayor satisfacción de los clientes interno o externos. — Menos accidentes
laborales. — Menos pérdidas de tiempo para buscar herramientas o papeles. — Una
mayor calidad del producto o servicio ofrecido. — Disminución de los
desperdicios generados. Las herramientas utilizadas en las 9 “s” son las
siguientes: — Diagrama de Causa – Efecto. — Listas de verificación. —
Entrevistas.
·
· Seiri:
Clasificación.
·
· Seiton:
Orden.
·
· Seiso:
Limpieza.
·
· Seiketsu:
Control visual (también con otras variantes como limpieza estandarizada).
·
· Shitsuke:
Disciplina.
·
· Objetivo
Central: “Lograr el funcionamiento más eficiente y uniforme de las personas en
los centros de trabajo.
1.- SEIRI. (Clasificación)
“Distinguir lo que es necesario de lo que no lo es, desechando lo
sobrante e identificando lo útil”. Otra buena práctica sería, colocar en un
lugar determinado todo aquello que va ser descartado. Y el último punto
importante es el de la clasificación de residuos. Generamos residuos de muy
diversa naturales: papel, plásticos, metales, etc.
Para poner en práctica la 1ra S debemos hacernos las siguientes
preguntas:
· ¿Qué debemos
tirar?
· ¿Qué debe ser
guardado?
· ¿Qué puede ser
útil para otra persona u otro departamento?
· 4. ¿Qué
deberíamos reparar? Para facilitar el proceso de identificar los elementos a
deshacerse, se tienen estas sugerencias: En dos años no se han
usado. Seguramente no se utilizaran en más de 3 años.
· De los que el
costo o incomodidad de tenerlos almacenados sea más alto que el de volverlo
adquirir. Pueden existir artículos en buenas condiciones, pero innecesarios
· Establecer un
área de desechos. Y, ¿dónde podemos detectar las cosas innecesarias?
· Lugares donde se
encuentran cosas que nadie usa o necesita.
· Repisas y casilleros.
· Pasillos y esquinas.
· Piezas y trabajo en
proceso.
· Herramientas, guías
e instrumentos de medición.
· Bajo las
escaleras y pilares.
· Paredes y pizarrón de
nota
2.- Seiton. (Ordenar) “Mantener las cosas necesarias
en forma: ordenada, identificadas y de fácil acceso, es decir, eliminar la
búsqueda de las cosas”. El orden se establece de acuerdo a los criterios
racionales, de tal forma que cualquier elemento esté localizable en todo
momento. Cada cosa debe tener un único, y exclusivo lugar donde debe
encontrarse antes de su uso, y después de utilizarlo debe volver a él.
El orden se lleva a cabo mediante la identificación de un
elemento, herramienta un objeto a través de un código, número o algo
característico de tal forma que sea fácil de localizar. Para tener claros los
criterios de colocación de cada cosa en su lugar, responderemos las siguientes
preguntas
· ¿Es posible
reducir el stock de esta cosa?
· ¿Esto es
necesario que esté a mano?
· ¿Todos llamaremos
a esto con el mismo nombre?
· ¿Cuál es el mejor
lugar para cada cosa? Y, ¿cómo los ordenamos? Definiendo el lugar de las
cosas y la forma de ordenarlas (lugar y forma).
·
· Ordenar
los artículos usando claves alfanuméricas.
·
· Determinar
los lugares de almacenamiento por periodos de utilización.
·
· Por
características: tamaño, color, función,
·
· Combinación
de métodos.
·
· Por:
función, producto o proceso. Durante este proceso, no te olvides de: Resaltar y
colocar marcas. Reducir exhibidores y repisas.
·
· Eliminar
alambres y conductos visibles.
·
· Colocar
las herramientas en el lugar en que se pueden tomar inmediatamente.
·
· Definir
espacios y contenedores especiales.
·
Colocar ayudas visibles
(letreros, indicaciones
. Seiso. (Limpieza) “Establecer métodos
para mantener limpio el lugar de trabajo”. Mantener permanentemente condiciones
adecuadas de aseo e higiene, lo cual no sólo es responsabilidad de la
organización sino que depende de la actitud de los empleados. La limpieza la
debemos hacer todos. Es importante que cada uno tenga asignada una pequeña zona
de su lugar de trabajo que deberá tener siempre limpia bajo su responsabilidad.
No debe haber ninguna parte de la empresa sin asignar. Si las persona no asumen
este compromiso la limpieza nunca será real.
Preguntas clave:
· 1.- ¿Existen
tuberías o líneas de suministro con aceite, polvo o de difícil acceso? 2.-
¿Cuánto aceite, polvo, mugre y pedazos de vidrio, plástico, papel o metal se
pueden encontrar?
· 3.- ¿Las salidas
de aceite están tapadas con tierra?
· 4.- ¿Están sucios
los focos, lámparas o pantallas?
Estrategia de limpieza en 4 pasos:
· Aspirar el polvo
del techo.
· Limpiar el piso.
· Quitar los
residuos y el moho.
· Pintar. Para
reforzar la limpieza:
· Asear el taller y
el equipo después de su uso.
· Pasar un trapo
sobre las herramientas.
· Sacar polvo y la
suciedad.
· Tener un programa
de limpieza.
4.- Seiketsu. Control visual (también con otras variantes como
estandarizar) “-Estandarizar: Establecer patrones y métodos que sean
fáciles de seguir y permitan hacerlo más sencillo. -Control Visual: Revelar
desperfectos a través de la estandarización de las actividades de las 5S.” Es
una forma empírica de distinguir una situación normal de una anormal, con
normas visuales para todos y establece mecanismos de actuación para reconducir
el problema.
Para comenzar, preguntémonos:
· 1.- ¿Cuáles son
los puntos de inspección cruciales?
· 2.- ¿Qué es lo
que se considera como un desperfecto?
· 3.- ¿Se puede
notar el desperfecto?
· 4.- ¿Qué tipo de
acciones son necesarias? Procedimiento:
·
5.- Shitsuke. (Disciplina) “Establecer
mecanismos para hacerlo un hábito”. Cada empleado debe mantener como hábito la
puesta en práctica de los procedimientos correctos. Sea cual sea la situación
se debe tener en cuenta que para cada caso debe existir un procedimiento.
Preguntas clave:
· 1.- ¿Se cuenta
con una inspección de vida cotidiana?
· 2.- ¿Se ejecutan
los reportes de órdenes de trabajo adecuadamente y en el tiempo correcto?
· 3.- ¿Se viste
correctamente la indumentaria de protección?
· 4.- ¿Se utilizan
correctamente cascos y gafetes?
Pasos:
·
Establecer Procedimientos Estándar de
Operación “POE´s”.
·
Preparar material didáctico y eventos de
instrucción.
·
Llegar a cada empleado involucrado, con
la técnica del “enseñar haciendo”, mostrarle como hacer.
·
Dejar que lo hagan y repetirlo hasta que haya
comprensión total y se adquiera el hábito.
·
Facilitar las condiciones para que cada
empleado ponga en práctica lo aprendido.
·
· Corregir
en el mismo puesto de trabajo, mientras se explica por qué no se hace así.
·
· Enseñar,
principalmente, con el ejemplo. Beneficios de utilizar las 5S.
·
· Cero
despilfarros, menores costos y capacidad más elevada.
·
· Cero
daños – mejora de la seguridad.
·
· Cero
averías – mejor mantenimiento.
·
· Cero
defectos – calidad más elevada.
·
· Cero
cambio de útiles – Facilitando la diversificación de la producción.
·
· Cero
retrasos – confiabilidad en las entregas.+
·
· Cero
quejas - aumento de la fiabilidad y la confianza.
·
· Cero
números rojos – crecimiento corporativo.
CLAVES PARA EL ÉXITO DE LAS 5S.
·
· Conseguir
implicar a todos.
·
· Obtener
autorización de la compañía.
·
· Hacer
que todos lo entiendan.
·
· La
responsabilidad final descansa en el presidente.
·
· Recorre
todo el camino.
·
· El
presidente debe inspeccionar la fábrica personalmente.
Las 5S, se han separado de las siguientes 4 debido a que es el método
más común utilizado en las empresas, pues debido a que implementar las 9 juntas
es un proceso más complejo, las 5S tienden a ser más flexibles y con excelentes
resultados si se realizan adecuadamente
6.- Shikari. (Constancia) Voluntad
para hacer las cosas y permanecer en ellas sin cambios de actitud, lo que
constituye una combinación excelente para lograr el cumplimiento de las metas
propuestas. Procedimiento · Planifique y controle permanentemente sus
trabajos. · Haga de la limpieza, el orden y la puntualidad una
constante en su vida. Ventajas 1. Se disminuye la cantidad de tiempo perdido,
si la voluntad para hacer las cosas se acompaña de motivación de los beneficios
de la meta
7.- Shitsukoku. (Compromiso) Es la
adhesión firme a los propósitos que se han hecho; es una adhesión que nace del
convencimiento que se traduce en el entusiasmo día a día por el trabajo a
realizar. Un compromiso que debe permear a todos los niveles de la empresa y
que debe utilizar el ejemplo como la mejor formación. Procedimiento. Se debe
llevar a cabo con disciplina aplicada de los dirigentes hacia sus subordinados.
Las políticas empresariales deben imponerse con seriedad para que el
empleado se sienta con una gran responsabilidad de llevar a cabo su trabajo.
Ventajas 1. El proyecto se llevará a cabo en el tiempo estimado sin pérdidas.
8.- Seishoo. (Coordinación) Una
forma de trabajar en común, al mismo ritmo que los demás y caminando hacia unos
mismos objetivos. Esta manera de trabajar sólo se logra con tiempo y
dedicación. Procedimiento · Mantener buena comunicación de los
avances como las demoras en tiempo. · Realizar mayor énfasis en la
etapa menos desarrollada. Ventajas 1. Permite un ambiente de trabajo
equilibrado, con mismos objetivos y metas.
9.- Seido.
(Estandarización) Permite regular y normalizar aquellos
cambios que se consideren benéficos para la empresa y se realiza a través de
normas, reglamentos o procedimientos. Éstos señalan cómo se deben hacer las
actividades que contribuyan a mantener un ambiente adecuado de trabajo.
Las 9S vienen a rescatar a la empresa del desorden y fomentar valores
que como en varias culturas no tenemos. Si bien, aunque fueron creadas en
Japón, no pueden quedarse exclusivamente ahí ya que han demostrado ser un
método muy eficaz en su implementación. La efectividad de las 9S, es de óptimo
rendimiento, la implementación de todas las reglas seguidas con seriedad, dan
como resultado alta eficacia y eficiencia, con sólo tener la disposición de
todos los involucrados. Los beneficios de la implantación de las 9S se podrán
notar en los niveles de productividad y calidad que se alcanzan dentro de la
organización. Y su mantenimiento residirá en la disciplina y constancia que se
tenga en la organización para la mejora continua de las actividades. Otro punto
a destacar es que el trabajo de investigación original, requería de las 11S,
del cual no se logró obtener alguna información o indicio sobre su existencia.
Si se comenta que apenas se están en proceso de su implementación, no existe
información aun al alcance para poder presentarlas en el presente trabajo.
6.5 APLICACIÓN
La aplicación de la mejora continua consiste en aplicar correctamente
los procedimientos dentro de las áreas de la organización. Es de vital
importancia seguir con orden los estándares aplicados a la calidad porque
de allí se puede definir el éxito para una empresa debido a que es de
vital importancia mantener en óptimas condiciones tanto el producto, como el
servicio para poder satisfacer las expectativas del cliente.
Comentarios
Publicar un comentario